|
Simulators for NPP
Multi-functional simulator is the training simulator, which Human-Machine Interface (HMI) realized by means of computer displays, mouse, light-pen or touch screen. Simulated facility process information presented on the graphical images and equipment can be controlled using mouse or light-pen.
The multi-functional simulators developed by SSL have complete and accurate mathematical models that simulate in real time all neutron-physical, thermo-hydraulic and electric processes of a power unit as well as all logic of I&C systems. The instructor subsystem included into the simulator provides the possibility to present a wide spectrum of emergency situations covering standard and specific malfunctions of all simulated equipment. Due to the above-mentioned features, the multi-functional simulator is identical to the full-scope one.
Even in case a full-scope simulator is available, the use of the multi-functional simulator in the process of operator training is fully justified as it allows to increase the efficiency of pre-simulator initial training, and thus reduces time and cost of training on the full-scope simulator.
The multi-functional simulator provides:
- initial training, retraining and continuing training of the NPP operating and engineering support personnel;
- training to operate the reactor, turbine and electrical departments of the power unit and control of their state in the normal and emergency modes;
- transients simulation and analysis of causes of emergencies taken place at NPP;
- verification of the operator’s actions correctness in transient modes described in the operating procedures;
- deep understanding of physical processes taking place in the operated object;
- analysis of plant technical and economic aspects with the purpose of their optimization;
- verification of symptom-oriented procedures;
- upgrade of the I&C systems;
- elaboration of training documentation.
SIMULATOR ARCHITECTURE
The simulator consists of an arbitrary set of modules carrying out specific tasks and exchanging data via the local network using a Common Data Area (further on referred to as CDA). The access to CDA is provided by means of the Server-module. The general architecture of the simulator is shown in figure.
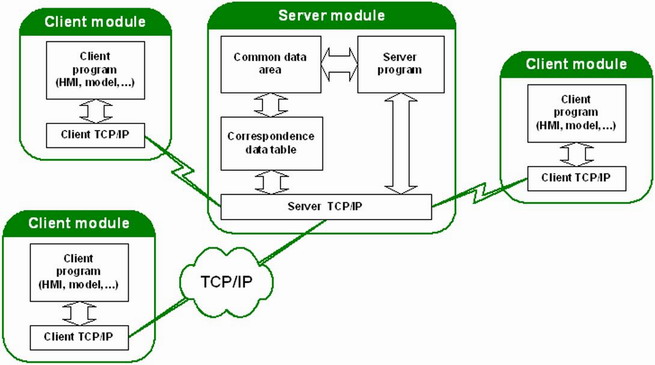
Depending on the capacity of the computers used and the complicity of the simulator models, the number of the computers-clients can be increased. At the same time, the computer-client can be used both for models operation and as an additional work place of the trainee.
The operating system Windows NT and the local network based on the TCP/IP protocol are used.
The programming language of the applications is Ñ++.
The mathematical simulation is based on:
- simulation of neutron processes in the reactor core in 3D representation;
- simulation of thermo-hydraulic processes in the core and the circulation loops on the basis of a distributed 3D two-phase and two-component model;
- simulation of the equipment, safety systems and the reactor department auxiliary systems using a network thermo-physical non-stationary approach;
- simulation of the equipment and the turbine department process systems using the network thermo-physical non-stationary approach; in order to simulate their dynamic behavior a non-stationary two-phase gas-dynamic system of conservative equations is used; presence of non-condensable gases in the steam-gas mixture is taken into account in the models of equipment;
- simulation of the I&C systems using the object-oriented programming, the encapsulation mechanisms and the multiple inheritance provided by Ñ++;
- simulation of the plant electric-power department using the network model based upon the Kirgoff’s laws as well as simulation of synchronous and asynchronous machines described by the Park-Gorev’s equations.
The simulators are developed in the integrated environment InSiDE created in SSL.
INSTRUCTOR’S SUBSYSTEM
The simulator training is done in the form of training sessions under the guidance of the instructor. The instructor works using the tools fulfilling the following functions:
- start simulation from the initial conditions supplied with the simulator, such as "cold state", "hot state", “nominal power state”, etc.;
- possibility to freeze simulation and restart from the "PAUSE" mode;
- possibility to save any simulator states, the so-called “Snapshots”, and to restart from any one of them during the training;
- possibility to define any saved snapshot as an initial condition for another training session;
- introduction of malfunctions set by the instructor during the training session or according to a preset scenario;
- modification of the boundary conditions (external parameters) during the training session;
- recording of the operator and the instructor actions with the possibility to print the data;
- control of the operator actions by the instructor with the possibility to interfere into the operation process;
- generating of false alarm signals, dispatcher or supervisor commands, etc.;
- acceleration of some specific processes (depending on the computer capacity);
- possibility of the whole system monitoring by the integral parameters;
- design of a new training session;
- possibility to output the preset dynamic parameters in a graphical form (to the computer display or to the printer) during the work of the simulator and their recording into a file for further analysis after training.
The simulator developed for Kalinin NPP is an example of the multi-functional simulators created by SSL.
|